-
WhatsAPP: +86 18706448138
-
Tengzhou, Shandong, China
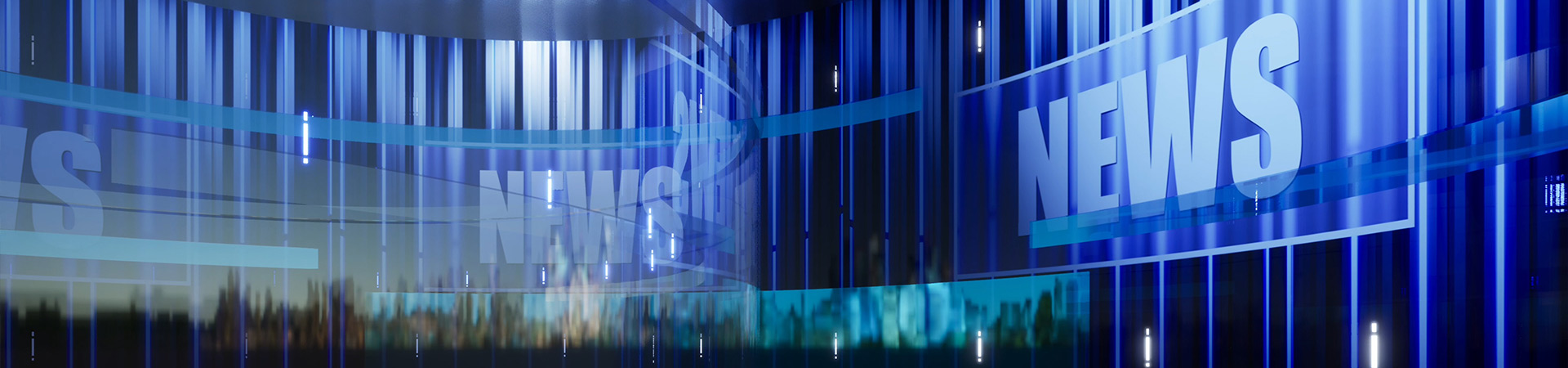
Your Guide to Selecting a CNC Control Panel
Whether you're a seasoned manufacturer or new to CNC technology, selecting the right CNC control panel is a critical decision that impacts your workflow.
Table of Contents
Introduction
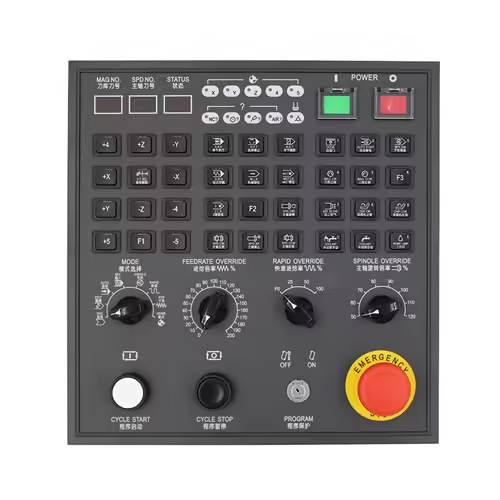
In the world of precision manufacturing, the CNC control panel serves as the heart of computer numerical control (CNC) machines, enabling operators to manage complex machining processes with accuracy and efficiency. A well-chosen CNC control panel can significantly enhance productivity, reduce errors, and streamline operations. Whether you’re a seasoned manufacturer or new to CNC technology, selecting the right CNC control panel is a critical decision that impacts your workflow and output quality. This guide, brought to you by Shansen, a leading developer and manufacturer of CNC machine electrical components since 2001, will walk you through the essential factors to consider when choosing a CNC control panel, ensuring you make an informed decision tailored to your needs.
What Is a Control Panel?
A CNC control panel is the interface between the operator and the CNC machine, allowing precise control over tools, movements, and machining parameters. It typically includes a display, keypad, and various input devices to program and execute commands. The control panel interprets the operator’s instructions, translates them into machine-readable code, and ensures the machine performs tasks like cutting, drilling, or milling with pinpoint accuracy. At Shansen, we’ve been designing control panels for over two decades, focusing on user-friendly interfaces and robust functionality to meet the demands of modern manufacturing.
Key Components of a Control Panel
Every control panel consists of several critical components that work together to deliver seamless operation. These include:
- Display Screen: Shows real-time data, tool paths, and programming interfaces.
- Keypad or Touchscreen: Allows operators to input commands and adjust settings.
- Control Buttons: Includes emergency stop, start, and pause functions for safety and control.
- Jog Wheels or Joysticks: Enables manual adjustments to machine movements.
- Communication Ports: Connects the control panel to the machine and external devices.
Understanding these components helps you evaluate whether a control panel meets your operational requirements.
Why Choosing the Right CNC Control Panel Matters
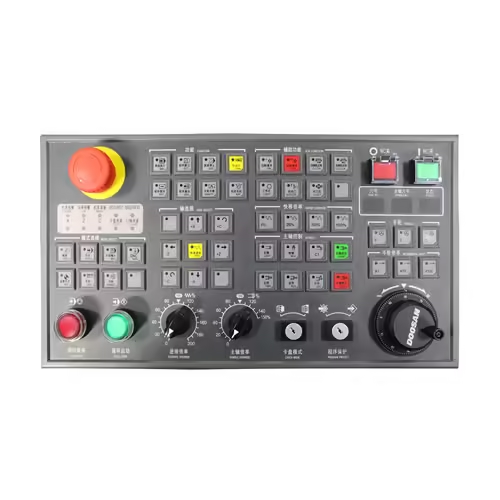
The CNC control panel directly influences the efficiency, precision, and safety of your machining processes. A poorly designed or incompatible CNC control panel can lead to programming errors, downtime, or even safety hazards. Conversely, a high-quality CNC control panel enhances operator confidence, reduces training time, and supports complex machining tasks. With Shansen’s expertise in manufacturing reliable control panels since 2001, we understand that selecting a panel that aligns with your machine’s capabilities and your production goals is essential for long-term success.
Impact on Productivity and Workflow
A well-designed control panel streamlines workflows by offering intuitive navigation, quick access to critical functions, and compatibility with advanced software. For example, modern control panels often support automation features, reducing manual intervention and boosting throughput. This is particularly important for industries like aerospace, automotive, and medical device manufacturing, where precision and speed are paramount.
Factors to Consider When Selecting a CNC Control Panel
Choosing the right control panel requires careful consideration of several factors. Below, we outline the most important aspects to evaluate to ensure your selection meets your operational needs.
Compatibility with Your CNC Machine
Not all CNC control panels are compatible with every CNC machine. Before purchasing, verify that the control panel supports your machine’s software, hardware, and communication protocols. For instance, older machines may require legacy control panels, while newer models might need panels with advanced connectivity options like Ethernet or USB. Shansen’s CNC control panels are engineered to integrate seamlessly with a wide range of CNC machines, ensuring compatibility and performance.
User Interface and Ease of Use
The CNC control panel’s user interface (UI) plays a significant role in operator efficiency. Look for panels with clear displays, logical menu structures, and customizable settings. Touchscreen control panels are increasingly popular for their intuitive navigation, but traditional keypad-based panels remain reliable for rugged environments. At Shansen, we prioritize ergonomic designs that minimize operator fatigue and reduce the learning curve.
Software Capabilities and Programming Flexibility
The software embedded in the control panel determines its programming capabilities. Advanced CNC control panels support G-code, conversational programming, and integration with CAD/CAM software. Some panels also offer simulation features to preview tool paths before machining begins, reducing errors. Ensure the control panel you choose supports the programming methods your team is familiar with and aligns with your production requirements.
Durability and Environmental Resistance
CNC control panels operate in demanding environments, often exposed to dust, coolant, and vibrations. Select a panel with robust construction, such as those with IP65-rated enclosures for water and dust resistance. Shansen’s control panels are built to withstand harsh industrial conditions, ensuring longevity and reliability.
Safety Features and Emergency Controls
Safety is non-negotiable in CNC operations. A reliable control panel should include easily accessible emergency stop buttons, fault detection systems, and override controls to prevent accidents. Check for certifications like CE or UL to ensure the panel meets industry safety standards.
Comparing CNC Control Panel Features
To help you evaluate different control panels, we’ve compiled a table summarizing key features to consider. This table is designed to guide your decision-making process without focusing on specific brands, ensuring a neutral and informative comparison.
Feature | Description | Why It Matters |
---|---|---|
Display Type | LCD, touchscreen, or LED display for showing machine status and programming data | Clear visuals reduce errors and improve operator efficiency. |
Input Method | Keypad, touchscreen, or jog wheel for entering commands | Affects ease of use and operator comfort during long shifts. |
Connectivity Options | USB, Ethernet, or RS-232 ports for connecting to machines and networks | Enables integration with modern software and automation systems. |
Programming Support | G-code, conversational programming, or CAD/CAM compatibility | Determines flexibility for complex or custom machining tasks. |
Durability Rating | IP rating (e.g., IP65) for resistance to dust, water, and vibrations | Ensures reliability in harsh manufacturing environments. |
Safety Features | Emergency stop, fault detection, and override controls | Protects operators and equipment from accidents and malfunctions. |
Customization Options | Ability to configure menus, shortcuts, or macros | Enhances workflow efficiency by tailoring the panel to specific needs. |
Simulation Capabilities | Previews tool paths and machining processes before execution | Reduces material waste and machining errors. |
Maintenance Requirements | Ease of cleaning, repair, or firmware updates | Lowers long-term operational costs and downtime. |
This table provides a framework for comparing CNC control panels based on your priorities, such as ease of use, durability, or advanced programming features.
Trends in CNC Control Panel Technology
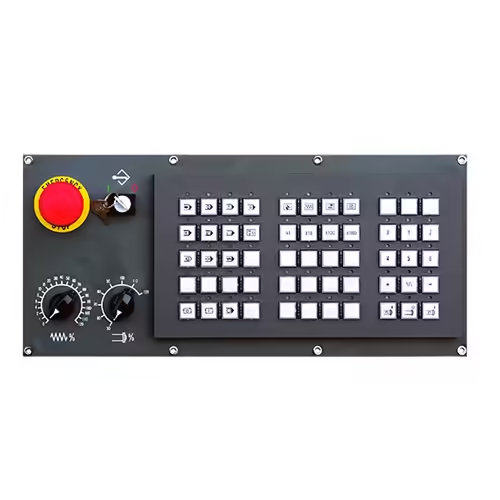
The control panel industry is evolving rapidly, driven by advancements in automation, connectivity, and user experience. Staying informed about these trends can help you select a forward-compatible control panel that supports future upgrades.
Integration with Industry 4.0
Modern CNC control panels are increasingly designed to support Industry 4.0 principles, such as real-time data monitoring, predictive maintenance, and cloud connectivity. These features allow manufacturers to optimize production, reduce downtime, and integrate with smart factory systems. Shansen’s latest control panels incorporate IoT-ready features to help you stay competitive in a connected manufacturing landscape.
Touchscreen and Gesture-Based Controls
Touchscreen control panels are becoming the standard due to their intuitive interfaces and ability to display complex data. Some advanced panels even support gesture-based controls, allowing operators to zoom, pan, or rotate tool path visualizations. These innovations enhance precision and reduce operator errors.
AI and Machine Learning Enhancements
Emerging CNC control panels are beginning to incorporate artificial intelligence (AI) and machine learning to optimize machining parameters automatically. For example, AI-driven control panels can adjust feed rates or spindle speeds in real-time based on material properties, improving efficiency and tool life.
How to Evaluate CNC Control Panel Suppliers
Selecting a CNC control panel is only part of the equation; choosing a reliable supplier is equally important. Here are some tips for evaluating suppliers:
- Experience and Reputation: Look for suppliers with a proven track record in CNC control panel manufacturing. Shansen, established in 2001, has built a reputation for delivering high-quality control panels trusted by manufacturers worldwide.
- Technical Support: Ensure the supplier offers robust technical support, including installation assistance, troubleshooting, and firmware updates.
- Customization Options: Some projects require tailored control panels. Choose a supplier that can customize panels to your specifications.
- Warranty and Service Agreements: Check for comprehensive warranties and maintenance services to protect your investment.
Common Mistakes to Avoid When Choosing a CNC Control Panel
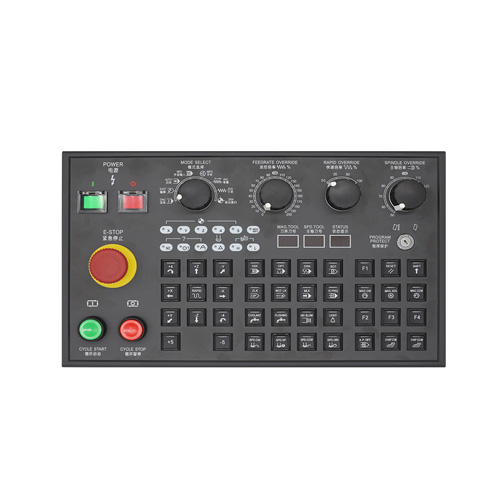
Even experienced manufacturers can make errors when selecting a CNC control panel. Avoid these common pitfalls to ensure a successful purchase:
- Ignoring Compatibility: Failing to verify compatibility with your CNC machine can lead to integration issues and costly retrofits.
- Overlooking Operator Training: A complex control panel may require extensive training, increasing onboarding time and costs.
- Focusing Solely on Price: While budget is important, prioritizing cost over quality can result in unreliable performance and frequent repairs.
- Neglecting Future Needs: Choose a control panel that supports future upgrades, such as additional axes or software enhancements, to avoid obsolescence.
Conclusion
Selecting the perfect CNC control panel is a pivotal decision that can elevate your manufacturing processes, improve efficiency, and ensure long-term reliability. By considering factors like compatibility, user interface, software capabilities, and durability, you can find a CNC control panel that meets your current needs and supports future growth. At Shansen, we’ve been empowering manufacturers with innovative control panels since 2001, and we’re here to help you make an informed choice. Ready to enhance your CNC operations? Contact us today to explore our range of CNC control panels and find the perfect solution for your business.
FAQ
What is the difference between a CNC control panel and a CNC controller?
A CNC control panel is the physical interface operators use to input commands and monitor operations, while the CNC controller is the internal system that processes those commands and drives the machine’s movements. The CNC control panel is essentially the user-facing component of the controller.
Can I upgrade my existing CNC control panel?
In many cases, yes, but it depends on your machine’s compatibility and the panel’s design. Consult with your supplier, like Shansen, to determine if an upgrade is feasible and cost-effective.
Are touchscreen CNC control panels better than keypad-based ones?
Touchscreen CNC control panels offer intuitive navigation and modern features, but keypad-based panels are often more durable in harsh environments. The choice depends on your specific needs and operating conditions.