-
WhatsAPP: +86 18706448138
-
Tengzhou, Shandong, China
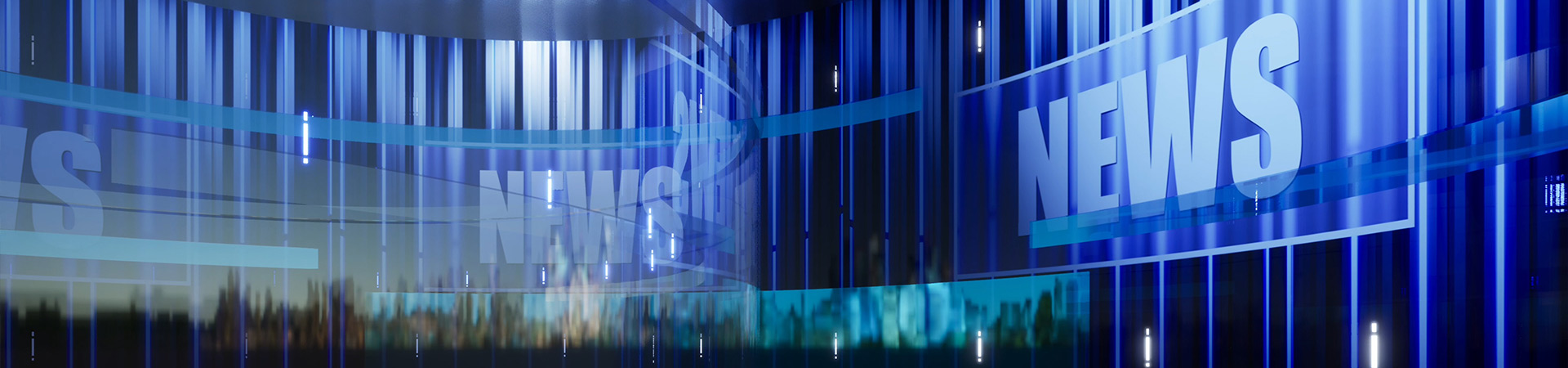
Compact Oil Mist Collector for CNC Machine Shops
This blog explores the importance, functionality, and benefits of using compact oil mist collectors in CNC machine shops.
Table of Contents
Introduction
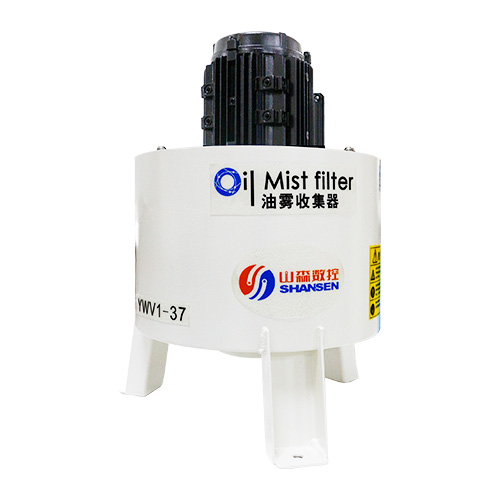
In the fast-paced world of CNC machining, maintaining a clean and safe work environment is critical for both operational efficiency and worker well-being. CNC machine shops often deal with oil mist and airborne contaminants generated during processes like milling, turning, grinding, and drilling. These tiny droplets, if not properly managed, can pose health risks, damage equipment, and lead to regulatory non-compliance. This is where a compact oil mist collector comes into play, offering an efficient, space-saving solution to capture and filter these hazardous particles. This blog explores the importance, functionality, and benefits of using compact oil mist collectors in CNC machine shops, providing a comprehensive guide for shop owners and operators looking to enhance their workplace.
Why CNC Machine Shops Need Compact Oil Mist Collectors
CNC machining processes involve high-speed cutting tools and metalworking fluids, which produce oil mist and smoke as byproducts. These airborne particles, ranging from 0.3 to 20 microns, can settle on machinery, floors, and surfaces, creating slippery hazards and increasing maintenance costs. A compact oil mist collector is designed to address these challenges by capturing mist at the source, ensuring cleaner air, safer working conditions, and prolonged equipment lifespan. Unlike traditional large filtration systems, these units are tailored for smaller spaces, making them ideal for modern CNC shops with limited floor space.
Health Risks of Uncontrolled Oil Mist in CNC Shops
Exposure to oil mist can lead to respiratory issues, skin irritation, and long-term health problems for workers. Inhalation of fine particles may cause conditions like bronchitis or dermatitis, while prolonged exposure can exacerbate asthma or other respiratory conditions. A compact oil mist collector mitigates these risks by filtering out harmful particles, ensuring compliance with OSHA and NIOSH standards, which set strict limits on airborne contaminants (e.g., 5 mg/m³ for oil mist). By prioritizing worker health, shops can reduce absenteeism and improve morale.
Environmental and Regulatory Compliance
Beyond health concerns, uncontrolled oil mist can lead to environmental violations. Regulatory bodies enforce stringent air quality standards, and non-compliance can result in fines or operational shutdowns. A compact oil mist collector helps CNC shops meet these regulations by capturing and filtering pollutants before they are released into the atmosphere. Many modern units also feature sustainable designs, such as reusable filters, which reduce waste and align with eco-friendly practices.
How Compact Oil Mist Collectors Work
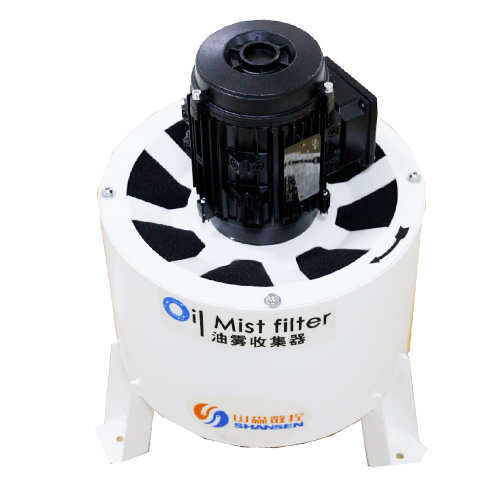
A compact oil mist collector operates by drawing contaminated air through a series of filtration stages. Typically, these systems use centrifugal force, media filters, or electrostatic precipitation to separate oil mist from the airstream. The process begins with an inlet that captures mist at the source, often directly mounted on the CNC machine. The air then passes through pre-filters to remove larger particles, followed by finer filters (e.g., HEPA or specialized mist filters) to capture submicron particles. Clean air is either recirculated into the shop or exhausted, while collected oil is drained for reuse or disposal.
Key Features of Compact Oil Mist Collectors
Modern compact oil mist collectors are engineered for efficiency and convenience. Key features include:
- High Filtration Efficiency: Capable of capturing particles as small as 0.3 microns with up to 99% efficiency.
- Space-Saving Design: Compact units fit easily in small CNC shops or on individual machines.
- Low Maintenance: Washable or long-lasting filters reduce replacement costs and downtime.
- Quiet Operation: Designed to minimize noise, ensuring a comfortable work environment.
- Modular Configurations: Many units offer customizable options to suit specific machining needs.
Benefits of Using Compact Oil Mist Collectors in CNC Operations
Implementing a compact oil mist collector in a CNC machine shop offers multiple advantages, from cost savings to improved productivity. These systems not only enhance air quality but also contribute to operational efficiency and equipment longevity.
Improved Machine Performance and Longevity
Oil mist buildup on CNC machine components can lead to corrosion, wear, and electronic malfunctions. By removing contaminants from the air, a compact oil mist collector prevents residue accumulation, reducing maintenance needs and extending machine life. This leads to fewer repairs, less downtime, and better return on investment for expensive CNC equipment.
Cost Savings on Maintenance and Energy
Uncontrolled oil mist can clog HVAC systems, increase cleaning costs, and lead to higher energy consumption due to over-exhausting air. Compact oil mist collectors recycle coolant back to the machine, reducing fluid waste, and return clean air to the shop, minimizing heating and cooling losses. These efficiencies translate to significant cost savings over time.
Enhanced Workplace Safety and Productivity
A cleaner shop environment reduces slip hazards and improves visibility, creating safer working conditions. Additionally, better air quality boosts employee productivity and morale, as workers are less likely to experience health issues or discomfort. Shops with compact oil mist collectors often report lower turnover and higher job satisfaction.
Choosing the Right Compact Oil Mist Collector for Your CNC Shop
Selecting the appropriate compact oil mist collector depends on several factors, including the type of CNC machines, coolant used, and shop size. Below is a table summarizing key considerations for choosing a collector:
Factor | Description | Consideration |
---|---|---|
Type of Coolant | Water-based, oil-based, or synthetic coolants produce different mist volumes. | Choose a collector suited for your coolant type (e.g., HEPA for fine particles). |
Airflow Capacity | Measured in cubic feet per minute (CFM), determines mist handling capability. | Match CFM to the mist output of your machines (e.g., 350–1200 CFM for most CNCs). |
Shop Size | Space constraints in smaller shops require compact, mountable units. | Opt for machine-mounted or wall-mounted collectors for limited spaces. |
Maintenance Needs | Frequency of filter cleaning or replacement impacts operational costs. | Select units with washable or long-life filters for reduced maintenance. |
Noise Level | High noise can disrupt shop operations. | Choose collectors with low decibel ratings (e.g., 60–66 dBA). |
Filtration Stages | Number of filtration stages affects efficiency. | Multi-stage systems (e.g., pre-filter, HEPA, carbon) offer higher efficiency. |
Matching Collectors to CNC Machine Types
Different CNC machines, such as lathes, mills, or Swiss screw machines, produce varying levels of mist. For example, high-pressure coolant systems in Swiss machines generate finer mist, requiring collectors with HEPA or electrostatic filters. Compact oil mist collectors are available in various models, such as ultra-compact units for single machines or larger systems for multiple setups, ensuring flexibility for diverse shop needs.
Budget and Long-Term Value
While compact oil mist collectors vary in price, their long-term value lies in reduced maintenance, compliance costs, and improved productivity. Investing in a high-quality unit with features like IoT monitoring or modular designs can save money by optimizing maintenance schedules and adapting to future needs.
Installation and Maintenance Tips for Compact Oil Mist Collectors
Proper installation and maintenance are crucial for maximizing the performance of a compact oil mist collector. Most units are designed for easy integration, with options for machine-mounted or wall-mounted setups. Ensure the collector is positioned to capture mist at the source, typically near the CNC machine’s enclosure. Regular maintenance, such as cleaning washable filters or replacing disposable ones, ensures consistent efficiency. Many modern collectors include monitoring systems that alert operators when filters need attention, reducing downtime.
Common Maintenance Practices
- Filter Cleaning/Replacement: Washable filters should be cleaned regularly, while disposable filters may need replacement every 6–12 months, depending on usage.
- Drainage Checks: Ensure the oil drainage system is functioning to prevent clogs and recycle coolant effectively.
- System Inspections: Periodically check for leaks or airflow issues to maintain optimal performance.
Advanced Technologies in Compact Oil Mist Collectors
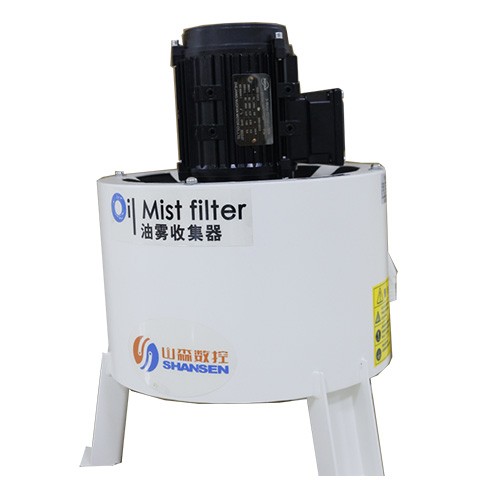
Recent advancements have made compact oil mist collectors more efficient and user-friendly. IoT-enabled systems provide real-time data on air quality and filter status, allowing remote monitoring and predictive maintenance. Modular designs offer scalability, enabling shops to adapt collectors to changing needs. Additionally, sustainable technologies, such as energy-efficient motors and recyclable filters, align with green manufacturing trends, reducing environmental impact.
IoT and Smart Monitoring
Smart compact oil mist collectors use sensors to track performance metrics, alerting operators to potential issues before they cause downtime. This technology improves operational efficiency and reduces maintenance costs by ensuring timely interventions.
Sustainable and Modular Designs
Modular collectors allow shops to customize filtration stages or airflow capacity, making them versatile for various CNC applications. Sustainable features, like reusable filters and energy-efficient motors, reduce operational costs and environmental footprint.
Conclusion
Compact oil mist collectors are indispensable for CNC machine shops aiming to maintain a safe, efficient, and compliant work environment. By addressing health risks, reducing maintenance costs, and enhancing machine performance, these systems deliver significant value. Their space-saving designs and advanced features, like IoT monitoring and sustainable filtration, make them a smart investment for shops of all sizes. To learn more about how a compact oil mist collector can transform your operations, contact us today for a tailored solution. Take the first step toward cleaner air and a more productive shop—contact us now!
FAQ
What is a compact oil mist collector?
A compact oil mist collector is a specialized air filtration system designed to capture and remove oil mist, coolant mist, and airborne particles generated during CNC machining processes, ensuring a clean and safe work environment.
How does a compact oil mist collector benefit CNC shops?
It improves air quality, reduces health risks, extends machine life, lowers maintenance costs, and ensures compliance with environmental and safety regulations.
What types of CNC machines need mist collectors?
Most CNC machines, including lathes, mills, grinders, and Swiss screw machines, benefit from mist collectors, especially those using high-pressure coolants.