-
WhatsAPP: +86 18706448138
-
Tengzhou, Shandong, China
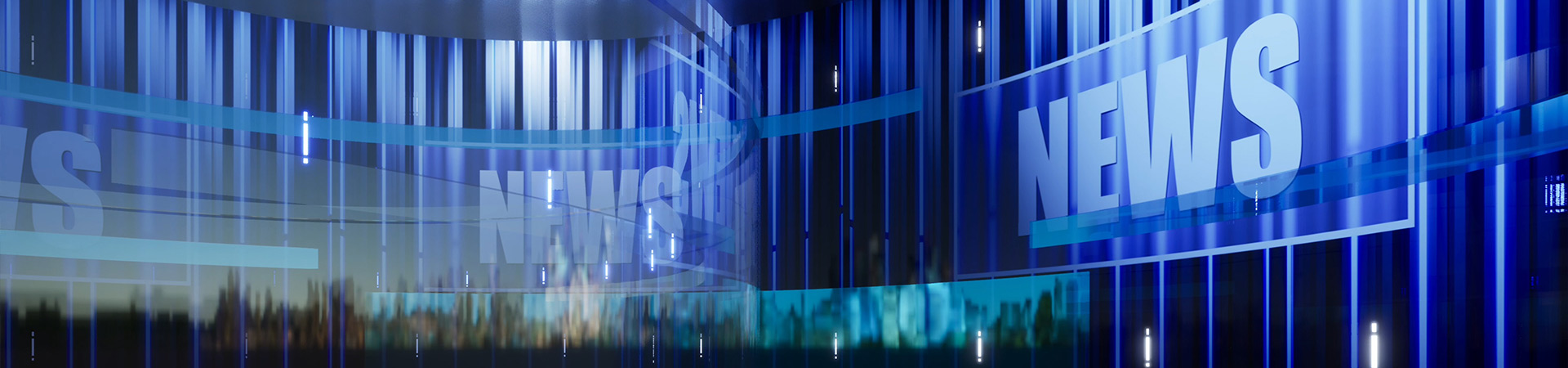
Explore the Benefits of a Precision Industrial Lathe
In this blog, we’ll explore the numerous benefits of using a precision industrial lathe, delving into its applications, features, and advantages.
Table of Contents
Introduction
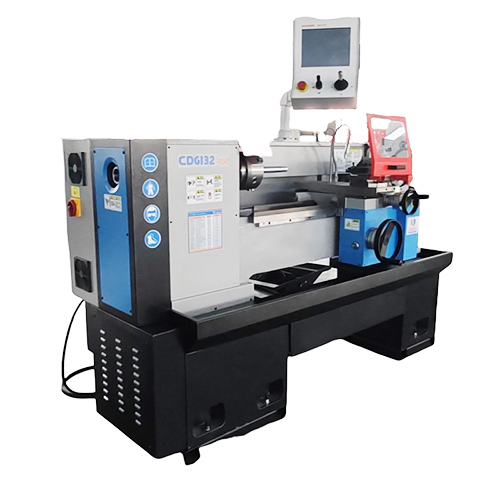
In modern manufacturing, achieving high accuracy and efficiency is paramount. Tools that deliver consistent, precise results are essential for industries ranging from aerospace to automotive. Among these tools, the industrial lathe stands out as a cornerstone of precision machining. This versatile machine shapes materials with unparalleled accuracy, making it indispensable for producing complex components. In this blog, we’ll explore the numerous benefits of using a precision industrial lathe, delving into its applications, features, and advantages for businesses aiming to enhance their production capabilities.
Why Precision Matters in Industrial Lathe Operations
Precision is the hallmark of quality in manufacturing. An lathe ensures components meet exact specifications, reducing errors and waste. By maintaining tight tolerances, these machines produce parts that fit seamlessly into larger assemblies, improving product reliability. Whether crafting intricate threads or smooth cylindrical surfaces, the precision of an industrial lathe enhances the overall quality of the final product, making it a critical asset for industries requiring meticulous craftsmanship.
Key Features of a Modern Lathe
Modern lathes are equipped with advanced features that elevate their performance. Computer Numerical Control (CNC) systems allow for automated, repeatable operations, minimizing human error. Variable speed controls and robust tooling options enable the machine to handle diverse materials, from metals to plastics. Additionally, many lathes include digital readouts and programmable settings, streamlining complex tasks and boosting productivity. These features make the lathe a versatile tool for both small workshops and large-scale factories.
Applications of Industrial Lathes Across Industries
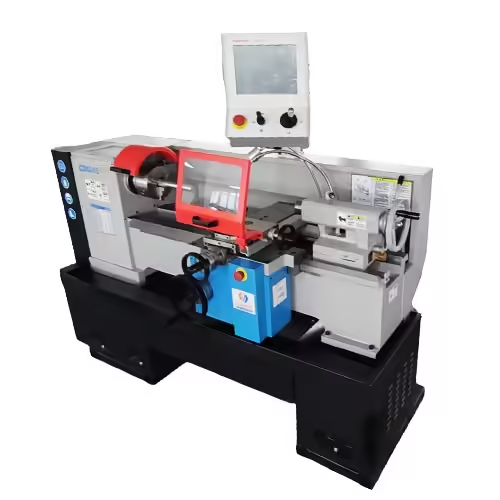
The versatility of an industrial lathe makes it a vital tool across multiple sectors. In aerospace, it crafts precision components like turbine shafts. In the automotive industry, it produces engine parts and suspension components. Medical device manufacturers rely on lathes for creating intricate implants and surgical tools. Even in energy sectors, such as oil and gas, industrial lathes shape durable parts for pipelines and drilling equipment. This broad applicability underscores the machine’s role in driving innovation and efficiency.
Enhancing Efficiency with an Lathe
Efficiency is a key benefit of using an industrial lathe. Automated CNC systems reduce setup times and allow for continuous operation, increasing throughput. The ability to perform multiple operations—such as turning, drilling, and threading—on a single machine minimizes the need for additional equipment, saving time and space. By optimizing workflows, an lathe helps businesses meet tight production schedules while maintaining high standards of quality.
Cost-Effectiveness of Investing in an Industrial Lathe
While the initial investment in an lathe may seem significant, the long-term savings are substantial. Precision machining reduces material waste, lowering raw material costs. The durability of modern lathes ensures minimal maintenance expenses, and their efficiency cuts labor costs by automating repetitive tasks. Over time, these savings translate into a strong return on investment, making the industrial lathe a cost-effective solution for manufacturers seeking to improve their bottom line.
Table: Key Specifications of a Typical Industrial Lathe
To provide a clearer understanding of what an lathe offers, the following table outlines typical specifications for a mid-range CNC lathe. These features highlight the machine’s capabilities and suitability for various applications.
Items | Parameter | Unit | CD6140 | CD6150 | CD6132 |
capacity | Swing over bed | mm | 400 | 500 | 330 |
Swing over cariage | mm | 230 | 290 | 160 | |
Center height | mm | 220 | 250 | 175 | |
Max. workpiece length | mm | 1000/1500/2000 | 1000/1500/2000/3000 | 750 | |
Max. processing length | mm | 950/1450/1950 | 950/1450/1950/2920 | 750 | |
Bed width | mm | 400 | 400 | 295 | |
Spindle | 3-jaw chuck diameter | mm | 200 | 250 | 160 |
Speed Gear | Stepless | Stepless | Stepless | ||
Speed ranges | rpm | 20-2000 | 16-1600 | 20-2600 | |
Spindle bore | mm | 58 | 82 | 43 | |
Spindle taper | mm | MT 6 | Metric 90 | MT 5 | |
Spindle nose | C6 | C8 | C5 | ||
Slides | Top slide travel | mm | 150 | 150 | 65 |
Cross travel(X axis) | mm | 260 | 260 | 190 | |
Longitudinal travel(Z axis) | mm | 1000/1500/2000 | 1000/1500/2000/3000 | 750 | |
Toolpost | Number of stations | 4 | 4 | 4 | |
Tool shank size | mm | 25X25 | 25X25 | 16 | |
Tailstock | Movement | Manual | Manual | Manual | |
Quill travel | mm | 160 | 160 | 130 | |
Quill diameter | mm | 75 | 75 | 60 | |
Quill taper | MT5 | MT5 | MT4 | ||
Feed | Rapid (Z/X axes) | mm/min | 3000/1500 | 3000/1500 | 3000/1500 |
X Cross feed (X axis) | mm/min | 15-1500 | 15-1500 | 15-1500 | |
Z Longitudinal feed (Z axis) | mm/min | 30-3000 | 30-3000 | 30-3000 | |
Movement per rotation/grade of top slide handwheel | mm/mm | 5/0.1 | 5/0.1 | 3/0.03 | |
Movement per rotation/grade ofcross slide handwheel (Xaxis) | mm/mm | 5/0.02 | 5/0.02 | 5/0.05 | |
Movement per rotation /grade oflongitudinal slide handwheel (Z axis) | mm/mm | 30/0.1 | 30/0.1 | 25/0.1 | |
Threads | Metric threads | mm | 0.25-24 | 0.25-24 | 0.25-24 |
Inch threads | in | 0.01-1 | 0.01-1 | 0.01-1 | |
Modular threads | mm | 0.08-8 | 0.08-8 | 0.08-8 | |
Diametrical threads | in | 0.01-0.32 | 0.01-0.32 | 0.01-0.32 | |
Motor | Servo spindle motor | kw | 5.5 | 7.5 | 3.7 |
Drive belt | Module | XPA2282 | XPA2282 | XPA1882 | |
Quantity | Pcs | 5 | 5 | 4 | |
Others | Length | mm | 2430/2930/3430 | 2430/2930/3430/4430 | 1900 |
Width x Height | mm | 1145×1740 | 1145×1740 | 850×1650 | |
Weight | kg | 2060/2210/2360 | 2130/2280/2430/2880 | 1260 |
This table illustrates the robust capabilities of an industrial lathe, making it a reliable choice for diverse manufacturing needs.
Safety Considerations When Operating an Lathe
Safety is critical when working with an lathe. Modern machines come equipped with safety features like emergency stop buttons, protective guards, and automatic shutoff systems. Operators must be trained to handle the equipment properly, wear appropriate protective gear, and follow safety protocols to prevent accidents. Regular maintenance checks ensure the lathe remains in optimal condition, reducing the risk of malfunctions that could compromise safety.
Environmental Benefits of Using an Lathe
In today’s eco-conscious world, manufacturers are seeking sustainable solutions. An lathe contributes to environmental responsibility by minimizing material waste through precise machining. Energy-efficient models reduce power consumption, lowering the carbon footprint of production processes. Additionally, the durability of these machines means fewer replacements, conserving resources over time. By adopting an lathe, businesses can align with green manufacturing practices while maintaining high productivity.
How to Choose the Right Lathe for Your Needs
Selecting the right industrial lathe depends on several factors, including production volume, material types, and desired precision. For small-scale operations, a manual lathe may suffice, while high-volume manufacturers benefit from CNC models. Consider the machine’s spindle speed, chuck size, and tool capacity to ensure it meets your requirements. Consulting with suppliers and reviewing technical specifications can help you find a lathe that aligns with your business goals.
Maintenance Tips for Maximizing Industrial Lathe Performance
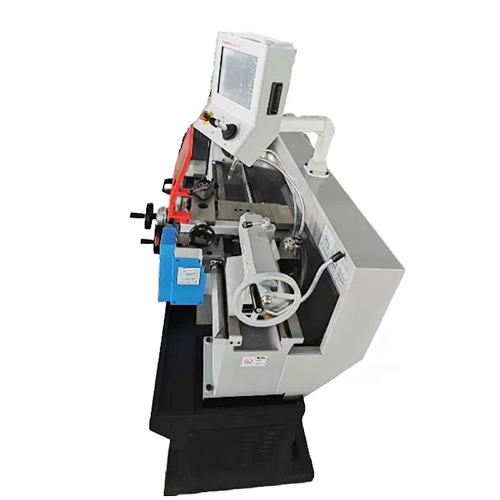
Regular maintenance is essential to keep an industrial lathe operating at peak performance. Lubricate moving parts to reduce friction and wear, and clean the machine to prevent debris buildup. Check alignment and calibration periodically to maintain precision. For CNC lathes, update software to ensure compatibility with new programs. Scheduling routine inspections by qualified technicians can identify potential issues early, extending the machine’s lifespan and ensuring consistent output.
Conclusion
The industrial lathe is a game-changer for manufacturers seeking precision, efficiency, and cost-effectiveness. Its versatility, advanced features, and ability to handle diverse applications make it an invaluable asset across industries. By investing in a high-quality lathe, businesses can enhance product quality, streamline operations, and achieve significant long-term savings. Ready to transform your production process? Contact us today to explore our range of precision industrial lathes and find the perfect solution for your needs.
FAQ
What materials can an industrial lathe process?
An industrial lathe can process a wide range of materials, including metals like steel, aluminum, and titanium, as well as plastics and composites, depending on the machine’s specifications and tooling.
How does a CNC industrial lathe differ from a manual lathe?
A CNC industrial lathe uses computer programming for automated, precise operations, while a manual lathe requires operator control, making it better suited for simpler tasks or low-volume production.
Can an industrial lathe be used for small-scale production?
Yes, smaller or manual industrial lathes are ideal for small-scale production, offering flexibility and precision for custom or low-volume projects.