-
WhatsAPP: +86 18706448138
-
Tengzhou, Shandong, China
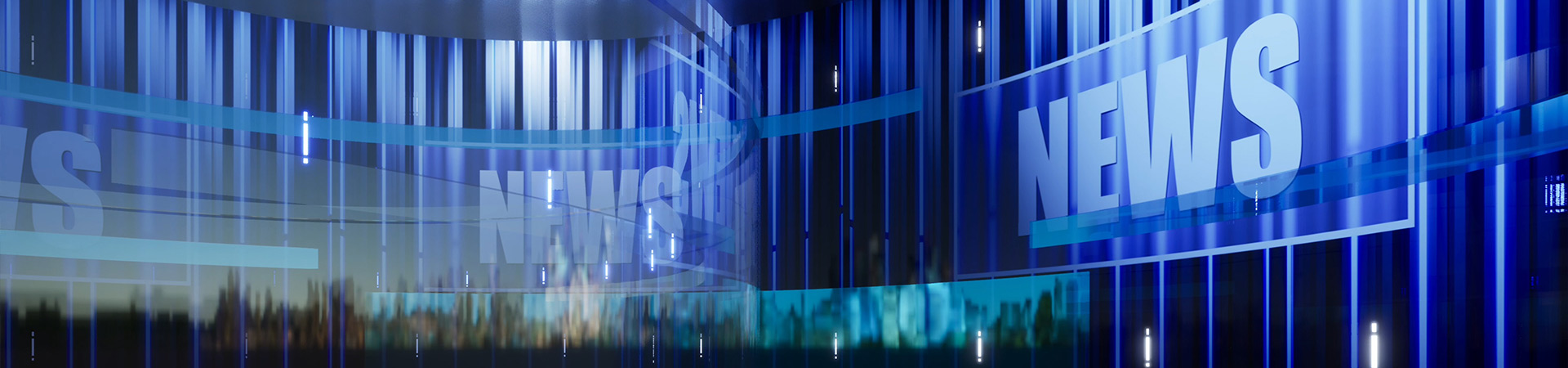
Oil Mist Collector System for CNC Machine Shops
An oil mist collector system is an essential tool designed to address these challenges by capturing and filtering oil mist before it spreads.
Table of Contents
Introduction
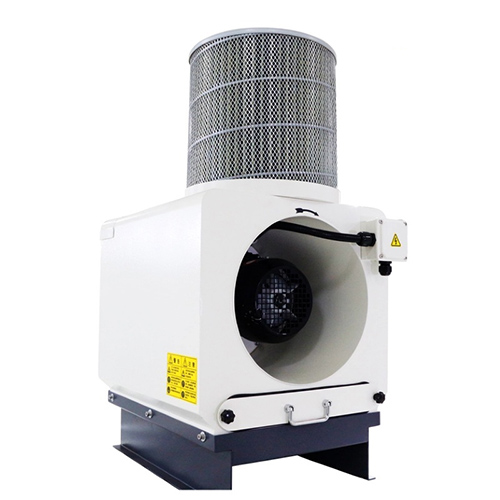
In the fast-paced world of CNC machining, maintaining a clean and safe working environment is critical for operational efficiency and worker health. CNC machine shops generate oil mist, a byproduct of machining processes that use cutting fluids or lubricants. This fine aerosol can pose significant health risks, damage equipment, and reduce workplace safety if not properly managed. An oil mist collector system is an essential tool designed to address these challenges by capturing and filtering oil mist before it spreads into the shop environment. This blog explores the importance, functionality, and benefits of implementing such systems in CNC machine shops, offering insights into how they can enhance productivity and ensure compliance with safety regulations.
Why Oil Mist is a Concern in CNC Machining
Oil mist forms during CNC operations when cutting fluids or lubricants are aerosolized due to high-speed machining, heat, or pressure. These tiny droplets, often invisible to the naked eye, can linger in the air, settle on surfaces, or be inhaled by workers. Prolonged exposure to oil mist can lead to respiratory issues, skin irritation, and other health concerns. Additionally, oil mist can coat machinery, leading to equipment wear, corrosion, or malfunctions. Slippery floors caused by settled mist also increase the risk of workplace accidents. An effective oil mist collector system mitigates these risks by capturing and removing the mist at its source, ensuring a safer and cleaner shop floor.
Health Risks Associated with Oil Mist Exposure
Workers in CNC machine shops are particularly vulnerable to the health hazards posed by oil mist. Inhalation of these particles can cause respiratory conditions such as bronchitis or occupational asthma. Skin contact with oil mist may result in dermatitis or other irritations. Regulatory bodies, such as OSHA, set strict guidelines for workplace air quality, and failure to comply can result in fines or operational shutdowns. By installing an oil mist collector system, shop owners can protect their workforce and maintain compliance with these standards, fostering a healthier work environment.
Environmental and Equipment Impacts
Beyond health concerns, oil mist can negatively affect the environment and machinery. Mist that settles on equipment can lead to costly repairs or replacements due to corrosion or clogged components. It can also contaminate HVAC systems, spreading pollutants throughout the facility. From an environmental perspective, improper disposal of oil mist can contribute to pollution if not handled correctly. An oil mist collector system captures these particles before they can cause harm, reducing maintenance costs and environmental impact while prolonging the lifespan of CNC machines.
How Oil Mist Collector Systems Work
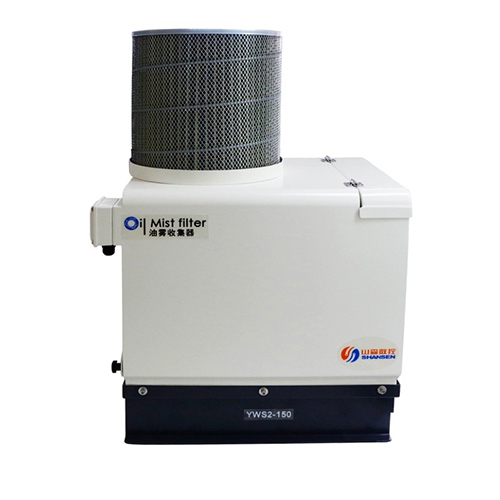
Oil mist collector systems are engineered to capture and filter oil mist generated during CNC machining. These systems typically consist of a series of filters, a fan or blower, and a collection mechanism. The process begins with the system drawing in contaminated air from the machining area. The air passes through multiple filtration stages, which may include pre-filters, main filters, and sometimes HEPA filters for ultra-fine particles. The cleaned air is then released back into the shop or vented outside, while the collected oil is either recycled or disposed of safely.
Key Components of an Oil Mist Collector System
The effectiveness of an oil mist collector system depends on its components. Pre-filters capture larger particles, protecting the main filtration system from clogging. The main filter, often a coalescing or electrostatic type, targets fine oil mist particles. Fans or blowers ensure consistent airflow, pulling contaminated air into the system. Some advanced systems include monitoring features to alert operators when filters need replacement or maintenance. Understanding these components helps shop owners choose a system that aligns with their specific machining needs.
Types of Oil Mist Collector Systems
There are several types of oil mist collector systems, each suited to different CNC applications. Centrifugal collectors use spinning motion to separate oil from air, ideal for high-volume mist production. Electrostatic precipitators use charged plates to attract and capture oil particles, offering high efficiency for fine mists. Media-based filtration systems rely on replaceable filters and are versatile for various machining processes. Selecting the right type depends on factors like mist volume, particle size, and shop layout.
Benefits of Implementing Oil Mist Collector Systems
Investing in an oil mist collector system offers numerous advantages for CNC machine shops. These systems improve air quality, reduce health risks, and enhance equipment longevity. They also contribute to regulatory compliance, helping shops avoid penalties. Additionally, cleaner air and surfaces create a more pleasant working environment, boosting employee morale and productivity. Over time, the reduction in maintenance costs and downtime can lead to significant financial savings.
Cost Savings and Efficiency Gains
While the initial investment in an oil mist collector system may seem significant, the long-term savings are substantial. By preventing equipment damage and reducing maintenance needs, these systems lower repair costs. Improved air quality also reduces the frequency of HVAC system cleanings. Furthermore, a cleaner shop floor minimizes downtime caused by accidents or equipment failures, allowing CNC machines to operate at peak efficiency.
Regulatory Compliance and Safety Standards
Compliance with workplace safety regulations is non-negotiable for CNC machine shops. Agencies like OSHA and NIOSH set strict limits on airborne contaminants, including oil mist. An oil mist collector system ensures that shops meet these standards, avoiding fines and protecting workers. Regular maintenance of these systems also demonstrates a commitment to safety, which can enhance a shop’s reputation and attract skilled employees.
Oil Mist Collector System Specifications Table
The following table outlines key specifications to consider when selecting an oil mist collector system for a CNC machine shop. This information can guide shop owners in choosing a system that meets their operational needs.
Feature | Description |
---|---|
Filtration Efficiency | Percentage of oil mist particles captured (e.g., 95% or higher for fine mist). |
Airflow Capacity | Volume of air processed per minute (CFM), typically 200–2000 CFM for CNC shops. |
Filter Type | Coalescing, electrostatic, or media-based filters for different mist types. |
Noise Level | Measured in decibels (dB), ideally below 70 dB for a comfortable work environment. |
Maintenance Frequency | How often filters need replacement or cleaning, typically every 6–12 months. |
Power Requirements | Voltage and wattage needed, often 110V or 220V for standard shop setups. |
Mounting Options | Floor-mounted, wall-mounted, or machine-mounted for flexible installation. |
This table provides a starting point for evaluating systems based on shop size, machining intensity, and budget constraints.
Installation Considerations for Oil Mist Collector Systems
Proper installation is critical to maximizing the performance of an oil mist collector system. Factors to consider include the system’s placement, ducting requirements, and integration with existing CNC machines. Systems should be positioned close to the mist source to capture particles effectively. Ducting must be properly sealed to prevent leaks, and airflow should be balanced to avoid disrupting machine operations. Consulting with a professional installer can ensure optimal setup and performance.
Space and Layout Planning
CNC machine shops vary in size and layout, so the oil mist collector system must fit within the available space. Compact systems are ideal for smaller shops, while larger facilities may require centralized units with extensive ducting. Wall-mounted or machine-mounted systems can save floor space, but they must be accessible for maintenance. Planning the layout in advance ensures seamless integration without compromising workflow.
Maintenance and Upkeep
Regular maintenance is essential to keep an oil mist collector system functioning effectively. This includes replacing or cleaning filters, checking fan performance, and inspecting ducting for blockages. Some systems come with digital monitoring tools that alert operators to maintenance needs, reducing the risk of downtime. Establishing a maintenance schedule can extend the system’s lifespan and ensure consistent air quality.
Choosing the Right Oil Mist Collector System for Your Shop
Selecting the appropriate oil mist collector system requires careful consideration of several factors. Shop owners should assess the volume of oil mist generated, the types of machining processes used, and the shop’s size. Budget constraints, ease of maintenance, and compatibility with existing equipment are also important. Consulting with suppliers or industry experts can help identify a system that balances performance and cost.
Evaluating System Performance
When evaluating an oil mist collector system, key performance metrics include filtration efficiency, airflow capacity, and energy consumption. High-efficiency systems capture a greater percentage of oil mist, while adequate airflow ensures consistent performance across multiple machines. Energy-efficient systems reduce operating costs, making them a smart choice for long-term use.
Customization Options for Specific Needs
Some CNC machine shops have unique requirements, such as handling high-viscosity oils or operating in extreme temperatures. Many oil mist collector systems offer customization options, such as specialized filters or adjustable airflow settings. These features allow shops to tailor the system to their specific machining processes, ensuring optimal performance and longevity.
Industry Trends in Oil Mist Collection Technology
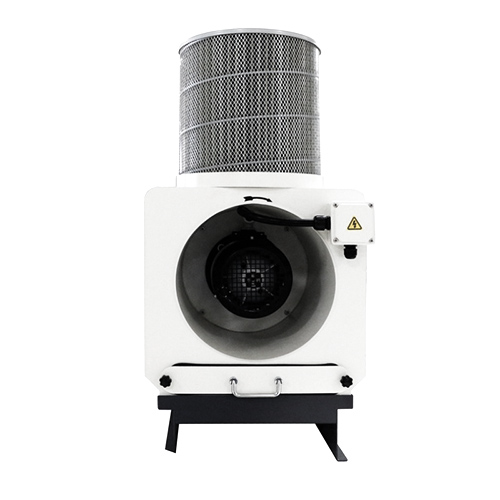
Advancements in oil mist collection technology are making these systems more efficient and user-friendly. Innovations include smart sensors that monitor filter conditions in real time, energy-efficient motors, and compact designs for smaller shops. Some systems now integrate with IoT platforms, allowing remote monitoring and predictive maintenance. Staying informed about these trends can help shop owners invest in future-proof solutions.
Sustainability and Eco-Friendly Designs
As environmental regulations tighten, manufacturers are developing oil mist collector systems with eco-friendly features. These include recyclable filters, energy-efficient components, and systems that allow for safe oil recycling. By choosing a sustainable system, CNC machine shops can reduce their environmental footprint while maintaining compliance with regulations.
Conclusion
An oil mist collector system is a vital investment for any CNC machine shop aiming to improve air quality, protect worker health, and enhance operational efficiency. By addressing the challenges of oil mist, these systems create a safer, cleaner, and more productive work environment. From reducing health risks to ensuring regulatory compliance, the benefits are clear. Ready to transform your shop? Contact us today to explore the best oil mist collector system for your needs and take the first step toward a cleaner future.
FAQ
What is an oil mist collector system?
An oil mist collector system is a filtration device that captures and removes oil mist generated during CNC machining, improving air quality and protecting equipment.
Can one system serve multiple CNC machines?
Yes, centralized oil mist collector systems with sufficient airflow capacity can service multiple machines, provided proper ducting is installed.
Are oil mist collector systems energy-intensive?
Modern systems are designed to be energy-efficient, with low-power motors and optimized airflow to minimize operating costs.