-
WhatsAPP: +86 18706448138
-
Tengzhou, Shandong, China
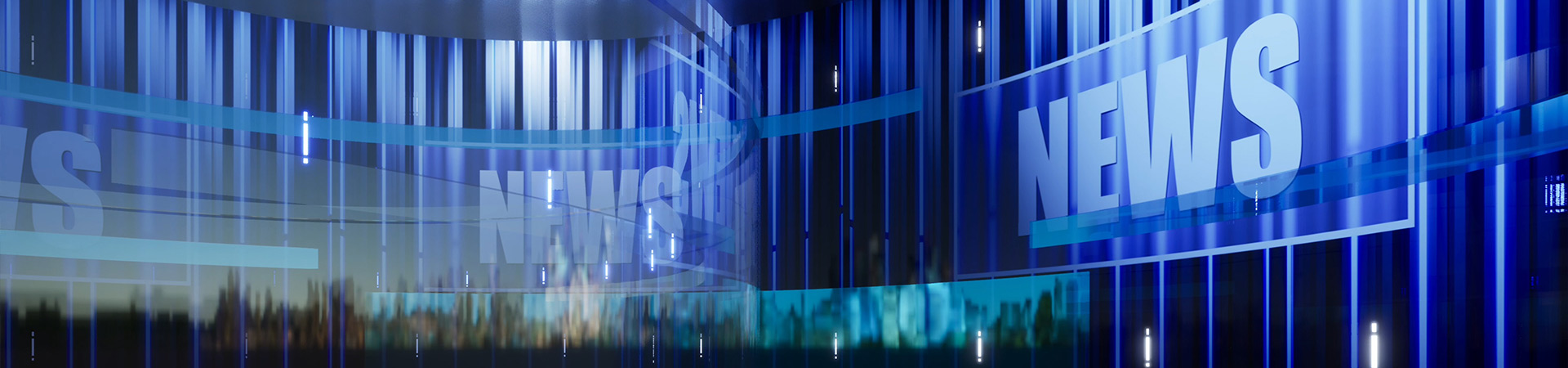
Cost-Effective Oil Mist Collector Systems Solutions
The implementation of effective oil mist collector systems has become paramount for ensuring a safe, clean, and productive working environment.
Table of Contents
Introduction
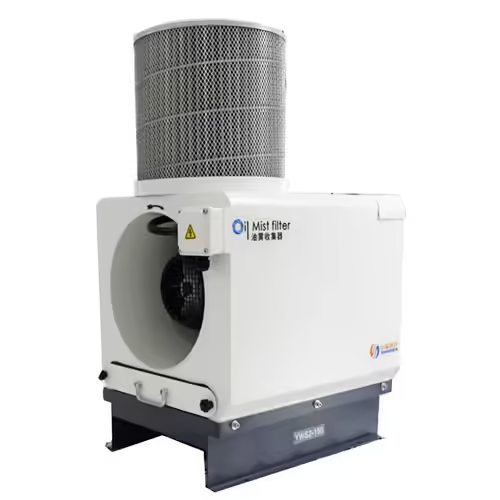
In the realm of modern manufacturing, particularly within industries utilizing Computer Numerical Control (CNC) machinery, the generation of oil mist is an unavoidable byproduct. This airborne particulate matter, composed of tiny oil droplets suspended in the air, poses significant risks to both human health and operational efficiency. Oil mist can lead to respiratory problems, skin irritation, and an increased risk of slips and falls. Furthermore, its accumulation on machinery and electrical components can cause malfunctions, reduce lifespan, and necessitate costly maintenance. Recognizing these challenges, the implementation of effective oil mist collector systems has become paramount for ensuring a safe, clean, and productive working environment. Shansen, a leading developer and manufacturer of electrical components for CNC machine tools, understands the critical importance of maintaining optimal operational conditions and offers insights into cost-effective solutions for managing oil mist.
Understanding the Necessity of Oil Mist Collector Systems
The presence of oil mist in manufacturing facilities extends beyond mere inconvenience. Its impact can be far-reaching, affecting employee well-being, equipment performance, and overall operational costs. Without efficient oil mist collector systems, airborne oil particles can permeate the workspace, leading to a range of adverse effects. For employees, prolonged exposure can result in respiratory ailments such as asthma, bronchitis, and hypersensitivity pneumonitis. Skin contact can cause dermatitis and other irritations. The slippery surfaces created by settling oil mist increase the likelihood of workplace accidents. From an operational standpoint, the accumulation of oil mist on sensitive electronic components within CNC machines can lead to short circuits, sensor failures, and reduced accuracy, ultimately impacting production quality and uptime. Regular cleaning and maintenance become more frequent and intensive, adding to operational expenses. Investing in effective oil mist collector systems is therefore not just an environmental or safety measure; it is a strategic decision that contributes directly to the long-term health and profitability of a manufacturing operation. Shansen recognizes that a clean working environment fostered by efficient oil mist collector systems is crucial for the optimal performance of CNC machinery and the well-being of the workforce.
Exploring Different Types of Oil Mist Collector Systems
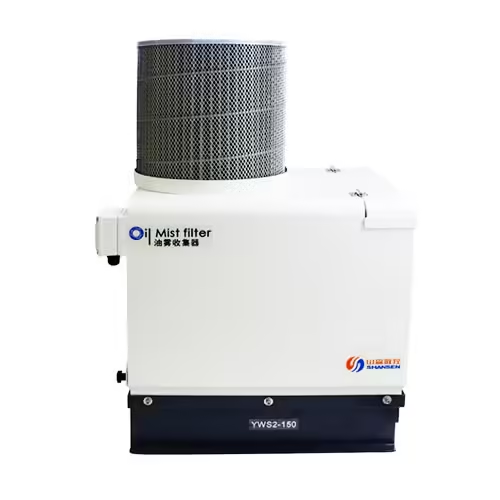
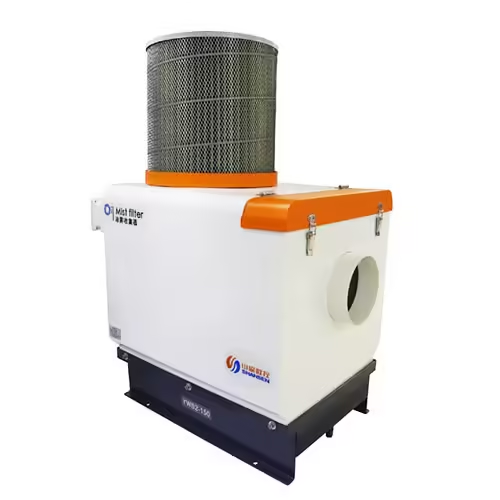
To effectively address the diverse needs of manufacturing environments, a variety of oil mist collector systems have been developed, each employing different filtration technologies and design principles. Understanding the characteristics and capabilities of these systems is crucial for selecting the most cost-effective and suitable solution. Some common types include:
- Mechanical Impingement Collectors: These systems utilize barriers or baffles to force oil mist particles to change direction abruptly. Due to inertia, the heavier particles impact the surfaces and coalesce into larger droplets that drain away. These systems are generally cost-effective for larger particle sizes and high oil mist concentrations.
- Coalescing Filters: Employing fibrous filter media, these systems capture fine oil mist particles through impaction and interception. The collected droplets then coalesce within the filter media and drain into a collection sump. Coalescing filters offer higher efficiency for smaller particle sizes compared to simple impingement collectors.
- Electrostatic Precipitators (ESPs): ESPs use an electric field to charge oil mist particles, which are then attracted to oppositely charged collection plates. The collected oil drains down the plates. ESPs offer high filtration efficiency for very fine particles and can have washable collection cells, reducing filter replacement costs.
- Media Filters: These systems utilize disposable or cleanable filter cartridges made of various materials like fiberglass or synthetic fibers. They offer high filtration efficiency for a wide range of particle sizes but require periodic replacement or cleaning, incurring ongoing operational costs.
- Centrifugal Collectors: These systems use centrifugal force generated by a rotating impeller to separate oil mist particles from the air stream. The heavier particles are thrown outwards and collected, while the cleaned air is exhausted. Centrifugal collectors are effective for high airflow applications and can handle significant oil mist loads.
The selection of the appropriate oil mist collector systems depends on factors such as the type and volume of oil mist generated, the required air quality, available space, and budget. Shansen, with its deep understanding of the manufacturing environment, can provide valuable insights into choosing the most suitable and cost-effective oil mist collector systems for specific applications.
Key Factors in Choosing Cost-Effective Oil Mist Collector Systems
When considering oil mist collector systems, cost-effectiveness extends beyond the initial purchase price. Several factors contribute to the overall economic viability of a solution. These include:
- Filtration Efficiency: A highly efficient system captures more oil mist particles, leading to a cleaner work environment and reduced maintenance on machinery. While systems with higher initial costs may offer superior filtration, it’s crucial to balance this with long-term operational savings.
- Maintenance Requirements: Systems with complex designs or requiring frequent filter replacements can incur significant ongoing costs. Opting for systems with easily cleanable or long-lasting filters can contribute to cost savings.
- Energy Consumption: Some oil mist collector systems, particularly those with high airflow rates, can consume significant amounts of energy. Choosing energy-efficient models can reduce operational expenses over the system’s lifespan.
- Durability and Reliability: Investing in robust and reliable oil mist collector systems from reputable manufacturers like those Shansen partners with can minimize downtime and the need for premature replacements.
- Scalability: As production needs evolve, the ability to expand or adapt the oil mist collector systems can be a significant cost-saving factor in the long run.
- Installation Costs: The complexity of installation can impact the overall cost. Choosing systems that are relatively easy to install can help minimize upfront expenses.
A comprehensive assessment of these factors is essential to identify the most cost-effective oil mist collector systems that meet the specific requirements of a manufacturing facility. Shansen’s expertise in the CNC machine tool industry allows them to advise on solutions that offer the optimal balance of performance, durability, and cost-efficiency.
Benefits of Implementing Efficient Oil Mist Collector Systems
The implementation of efficient oil mist collector systems yields a multitude of benefits that contribute to a more productive, safer, and cost-effective manufacturing operation. These advantages include:
- Improved Air Quality: Effective filtration removes harmful oil mist particles from the air, creating a healthier and more comfortable working environment for employees. This can lead to reduced respiratory issues and improved morale.
- Enhanced Workplace Safety: By eliminating slippery surfaces caused by settling oil mist, the risk of slips, trips, and falls is significantly reduced, contributing to a safer work environment and potentially lowering insurance costs.
- Reduced Machinery Maintenance: Preventing the accumulation of oil mist on sensitive machine components minimizes the risk of malfunctions, extends the lifespan of equipment, and reduces the frequency and cost of maintenance.
- Increased Productivity: A cleaner and healthier work environment can lead to improved employee focus and reduced absenteeism, ultimately boosting overall productivity. Properly functioning machinery, free from oil mist contamination, also contributes to smoother operations and higher output.
- Compliance with Environmental Regulations: Many regions have regulations regarding airborne contaminants in industrial environments. Implementing effective oil mist collector systems helps ensure compliance and avoids potential fines or legal issues.
- Energy Savings: Some advanced oil mist collector systems are designed with energy efficiency in mind, helping to reduce overall energy consumption and lower operating costs.
- Improved Product Quality: By preventing oil mist from settling on workpieces, the risk of contamination and defects is minimized, leading to higher product quality and reduced scrap rates.
Shansen understands that investing in efficient oil mist collector systems is not just an expense but a strategic investment that delivers significant returns in terms of operational efficiency, employee well-being, and long-term cost savings.
Cost Analysis of Different Oil Mist Collector Systems
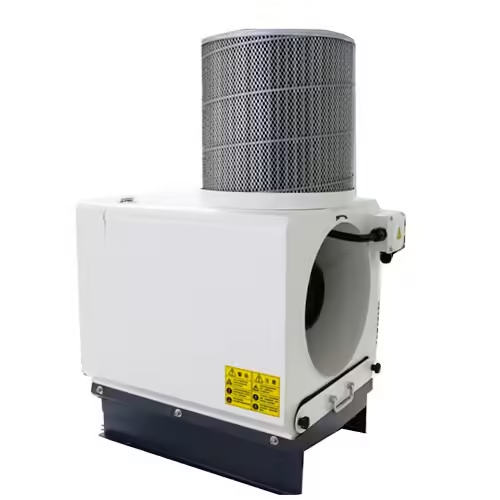
A thorough cost analysis is crucial when selecting oil mist collector systems. This analysis should consider not only the initial purchase price but also the long-term operational costs associated with each type of system.
System Type | Initial Cost | Filtration Efficiency | Maintenance Requirements | Energy Consumption | Lifespan |
---|---|---|---|---|---|
Mechanical Impingement | Low | Low to Medium | Low | Low | Long |
Coalescing Filters | Medium | Medium to High | Medium | Low to Medium | Medium to Long |
Electrostatic Precipitators | High | High | Medium to High (cleaning) | Medium | Long |
Media Filters | Medium | High | High (filter replacement) | Low to Medium | Medium |
Centrifugal Collectors | Medium to High | Medium to High | Low | Medium to High | Long |
It’s important to note that these are general comparisons, and specific costs can vary depending on the manufacturer, size, and features of the oil mist collector systems. A detailed cost-benefit analysis, considering the specific needs and operational context of the manufacturing facility, is recommended to make an informed decision. Factors such as filter replacement costs, energy consumption rates, and potential savings from reduced maintenance and improved productivity should be factored into the equation. Shansen can assist in evaluating these factors to help identify the most cost-effective oil mist collector systems for your specific needs.
Conclusion
In conclusion, the implementation of cost-effective oil mist collector systems is an indispensable investment for modern manufacturing facilities. Beyond ensuring a safe and healthy working environment, these systems contribute significantly to operational efficiency, reduced maintenance costs, and compliance with environmental regulations. By carefully considering the various types of oil mist collector systems, evaluating key factors such as filtration efficiency, maintenance requirements, and energy consumption, and conducting a thorough cost analysis, businesses can identify the most suitable and economically viable solutions for their specific needs. Shansen, as a leading developer and manufacturer of electrical components for CNC machine tools, recognizes the critical role of clean air in optimizing machine performance and employee well-being. Don’t compromise on the health of your workforce and the efficiency of your operations. Contact us today to explore our range of cost-effective oil mist collector systems solutions and take a step towards a cleaner, safer, and more productive future.
FAQ
Q: What are the primary benefits of using oil mist collector systems?
A: The primary benefits include improved air quality, enhanced workplace safety, reduced machinery maintenance, increased productivity, compliance with environmental regulations, potential energy savings, and improved product quality.
Q: How do I choose the right oil mist collector systems for my application?
A: The selection depends on factors such as the type and volume of oil mist generated, the required air quality, available space, budget, and specific application requirements. Consulting with experts like Shansen can help in making the right choice.
Q: What are the different types of oil mist collector systems available?
A: Common types include mechanical impingement collectors, coalescing filters, electrostatic precipitators (ESPs), media filters, and centrifugal collectors.