-
WhatsAPP: +86 18706448138
-
Tengzhou, Shandong, China
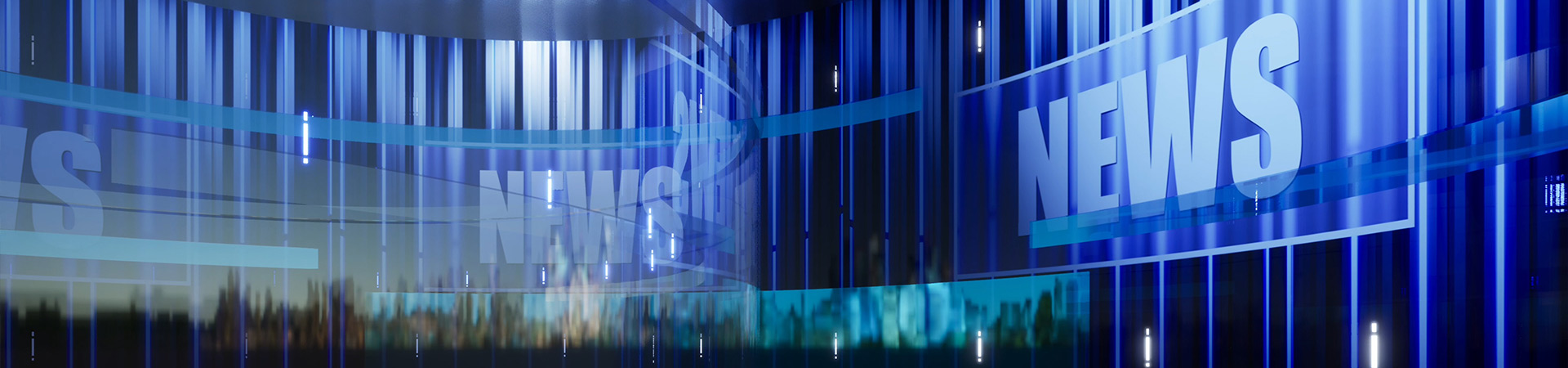
Electronic Lathe: High-Speed, Accurate Cutting
This blog explores the capabilities and applications of electronic lathes, providing insights into why they are essential for businesses aiming.
Table of Contents
Introduction
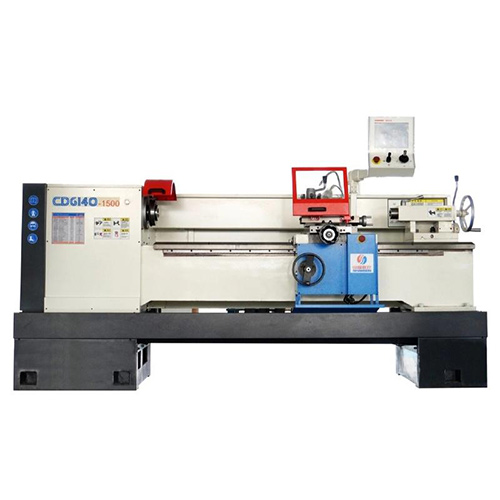
The electronic lathe represents a significant advancement in modern machining, combining precision, speed, and automation to meet the demands of industries ranging from aerospace to automotive. Unlike traditional lathes, an electronic lathe integrates digital controls and advanced software to deliver high-speed, accurate cutting, making it a cornerstone of contemporary manufacturing. This blog explores the capabilities, benefits, and applications of electronic lathes, providing insights into why they are essential for businesses aiming to optimize production processes. Whether you’re a seasoned machinist or a business owner exploring new equipment, understanding the electronic lathe’s role in achieving precise and efficient results is crucial.
What Is an Electronic Lathe?
An electronic lathe is a computer-controlled machine tool designed for shaping materials such as metal, wood, or plastic through high-speed, accurate cutting. It uses a combination of servo motors, digital interfaces, and programmable logic controllers (PLCs) to execute complex machining tasks with minimal human intervention. The electronic lathe stands out for its ability to maintain tight tolerances, often within micrometers, ensuring consistent quality across large production runs. By leveraging advanced electronics, these lathes can perform intricate operations like threading, turning, and facing with exceptional precision, making them indispensable in modern workshops.
Key Components of an Electronic Lathe
The electronic lathe comprises several critical components that enable its high-performance capabilities. The spindle, driven by a powerful motor, rotates the workpiece at variable speeds, which can be adjusted via a digital control panel. The tool turret, another vital feature, holds multiple cutting tools, allowing seamless transitions between operations. Additionally, the electronic lathe’s control system, often a CNC (Computer Numerical Control) interface, enables operators to program complex cutting paths. These components work in harmony to ensure the machine delivers accurate cuts at high speeds, reducing cycle times and improving productivity.
How Electronic Lathes Differ from Traditional Lathes
Traditional lathes rely heavily on manual operation, requiring skilled machinists to adjust settings and monitor the cutting process. In contrast, an electronic lathe automates these tasks through programmable controls, reducing the need for constant operator oversight. This automation not only enhances accuracy but also allows for faster setup times and the ability to handle complex geometries. The integration of digital technology in electronic lathes also enables real-time monitoring and adjustments, ensuring consistent performance even during extended operations. This makes electronic lathes ideal for industries requiring high-speed, accurate cutting.
Benefits of Using an Electronic Lathe for High-Speed Cutting
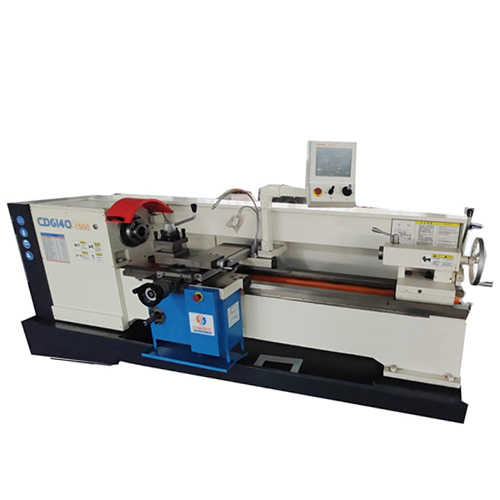
The electronic lathe offers numerous advantages for manufacturers seeking efficiency and precision. Its ability to operate at high speeds without sacrificing accuracy makes it a preferred choice for producing intricate parts. Additionally, electronic lathes reduce material waste by optimizing cutting paths, which lowers production costs. The automation features also minimize human error, ensuring consistent quality across batches. For businesses, this translates to faster turnaround times and the ability to meet tight deadlines, making the electronic lathe a valuable asset in competitive markets.
Enhanced Precision with Electronic Lathe Systems
Precision is a hallmark of the electronic lathe, thanks to its advanced control systems. These machines can maintain tolerances as tight as ±0.001 mm, making them suitable for applications where accuracy is non-negotiable, such as medical device manufacturing or aerospace components. The CNC interface allows operators to input precise measurements and cutting parameters, which the electronic lathe executes flawlessly. This level of precision ensures that even the most complex parts meet stringent quality standards, reducing the need for rework and enhancing overall efficiency.
Increased Productivity Through Automation
Automation is a key driver of productivity in electronic lathes. By programming repetitive tasks, manufacturers can produce large volumes of parts with minimal manual intervention. The electronic lathe’s ability to switch between tools automatically and adjust cutting speeds in real time further boosts throughput. For example, a single electronic lathe can complete multiple operations—such as turning, drilling, and threading—in one setup, eliminating the need for multiple machines. This streamlined workflow is particularly beneficial for high-volume production environments.
Applications of Electronic Lathes in Modern Industries
Electronic lathes are versatile tools used across various industries to produce components with high precision and efficiency. In the automotive sector, they are employed to manufacture engine parts, shafts, and gears, where high-speed, accurate cutting is essential. Aerospace manufacturers rely on electronic lathes to create lightweight, durable components like turbine blades. Additionally, the electronics industry uses these machines to produce intricate parts for devices, ensuring tight tolerances and smooth finishes. The adaptability of electronic lathes makes them suitable for both small-scale workshops and large-scale industrial facilities.
Electronic Lathes in Aerospace Manufacturing
In aerospace, where safety and precision are paramount, the electronic lathe plays a critical role. These machines are used to produce components like landing gear parts and engine housings, which require exact dimensions and flawless surface finishes. The high-speed cutting capabilities of electronic lathes allow manufacturers to work with tough materials like titanium and composites, maintaining accuracy even at elevated speeds. This ensures that aerospace parts meet rigorous industry standards, contributing to the safety and reliability of aircraft.
Automotive Industry Applications
The automotive industry benefits significantly from the electronic lathe’s ability to produce high-quality parts quickly. Components such as crankshafts, camshafts, and transmission gears require precise machining to ensure optimal performance. The electronic lathe’s programmable controls allow for rapid production of complex parts, reducing lead times and enabling manufacturers to meet the automotive industry’s high demand for precision components. This makes electronic lathes a key tool in automotive production lines.
Technical Specifications for Electronic Lathe Cutting
To provide a clearer understanding of the capabilities of electronic lathes, the following table outlines typical technical specifications for high-speed, accurate cutting. These specifications vary depending on the machine’s size and intended application but offer a general overview of what to expect from a modern electronic lathe.
Feature | Specification |
---|---|
Spindle Speed | 50–6,000 RPM |
Maximum Workpiece Diameter | Up to 500 mm |
Maximum Cutting Length | Up to 1,500 mm |
Tool Turret Capacity | 8–12 tools |
Control System | CNC with touchscreen interface |
Accuracy | ±0.001 mm |
Motor Power | 5–15 kW |
Feed Rate | 0.01–2,000 mm/min |
Weight | 2,000–5,000 kg |
This table highlights the key features that enable electronic lathes to deliver high-speed, accurate cutting, making them suitable for a range of materials and applications.
Optimizing Electronic Lathe Performance
To maximize the performance of an electronic lathe, operators must focus on several factors, including tool selection, cutting parameters, and maintenance. High-speed steel (HSS) or carbide tools are commonly used for their durability and ability to withstand high temperatures. Proper programming of the CNC system is also critical, as it determines the cutting path and speed. Regular maintenance, such as checking spindle alignment and lubricating moving parts, ensures the electronic lathe operates at peak efficiency.
Selecting the Right Cutting Tools
Choosing the appropriate cutting tools is essential for achieving high-speed, accurate cutting with an electronic lathe. Carbide tools are preferred for their hardness and ability to maintain sharp edges during high-speed operations. For softer materials like aluminum, high-speed steel tools may suffice, offering cost savings without compromising performance. Operators should also consider tool geometry, as the angle and shape of the cutting edge impact the quality of the finish and the speed of the cut.
Programming for High-Speed Cutting
Effective programming is the backbone of electronic lathe performance. CNC software allows operators to input detailed instructions for cutting paths, speeds, and feeds, ensuring the machine operates efficiently. For high-speed cutting, programmers should prioritize smooth tool paths to minimize vibrations and optimize feed rates to balance speed and accuracy. Advanced electronic lathes often include simulation features, allowing operators to test programs virtually before running them, reducing the risk of errors.
Safety Considerations for Operating Electronic Lathes
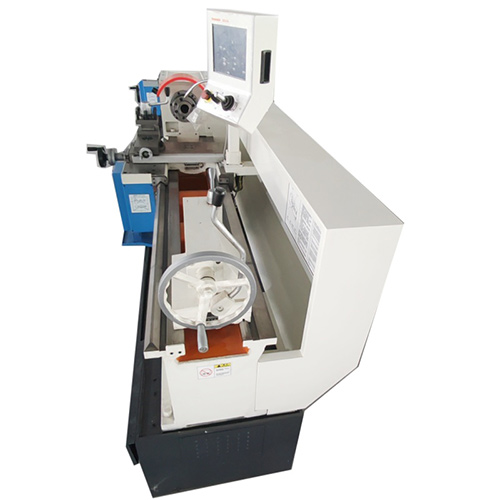
Safety is a top priority when operating an electronic lathe, given the high speeds and powerful components involved. Operators must be trained to use the machine’s control systems and understand safety protocols, such as wearing protective gear and securing workpieces properly. The electronic lathe’s automation features, like emergency stop functions and safety interlocks, help prevent accidents. Regular inspections of the machine’s electrical systems and cutting tools are also essential to ensure safe operation.
Training Operators for Safe Use
Proper training is critical for safe and effective operation of an electronic lathe. Operators should be familiar with the machine’s control interface, including how to program and troubleshoot common issues. Training programs should also cover safety practices, such as how to handle high-speed cutting tools and what to do in case of a malfunction. Many manufacturers offer training courses tailored to specific electronic lathe models, ensuring operators are well-equipped to handle the equipment.
Maintenance for Safe and Reliable Performance
Regular maintenance is vital to keep an electronic lathe running safely and efficiently. This includes routine checks of the spindle, tool turret, and control system to identify wear or potential issues. Lubrication of moving parts reduces friction and prevents overheating, while cleaning the machine removes debris that could interfere with high-speed cutting. Scheduled maintenance not only enhances safety but also extends the lifespan of the electronic lathe, ensuring long-term reliability.
Conclusion
The electronic lathe is a game-changer for manufacturers seeking high-speed, accurate cutting in today’s competitive landscape. Its advanced control systems, automation features, and versatility make it an essential tool for industries ranging from aerospace to automotive. By delivering precision, efficiency, and reliability, electronic lathes enable businesses to meet stringent quality standards and tight production schedules. For those looking to elevate their machining capabilities, investing in an electronic lathe is a strategic move. Contact us today to explore how an electronic lathe can transform your production process and drive success.
FAQ
What materials can an electronic lathe process?
An electronic lathe can process a wide range of materials, including metals (steel, aluminum, titanium), plastics, and wood. The choice of cutting tools and parameters determines the machine’s suitability for specific materials.
How does an electronic lathe ensure accuracy?
The electronic lathe ensures accuracy through its CNC control system, which allows precise programming of cutting paths and speeds. High-quality components, such as servo motors and precision bearings, also contribute to its ability to maintain tight tolerances.
Can electronic lathes be used for small-scale production?
Yes, electronic lathes are versatile and can be used for both small-scale and large-scale production. Their programmable controls make them suitable for prototyping and custom projects, as well as high-volume manufacturing.