-
WhatsAPP: +86 18706448138
-
Tengzhou, Shandong, China
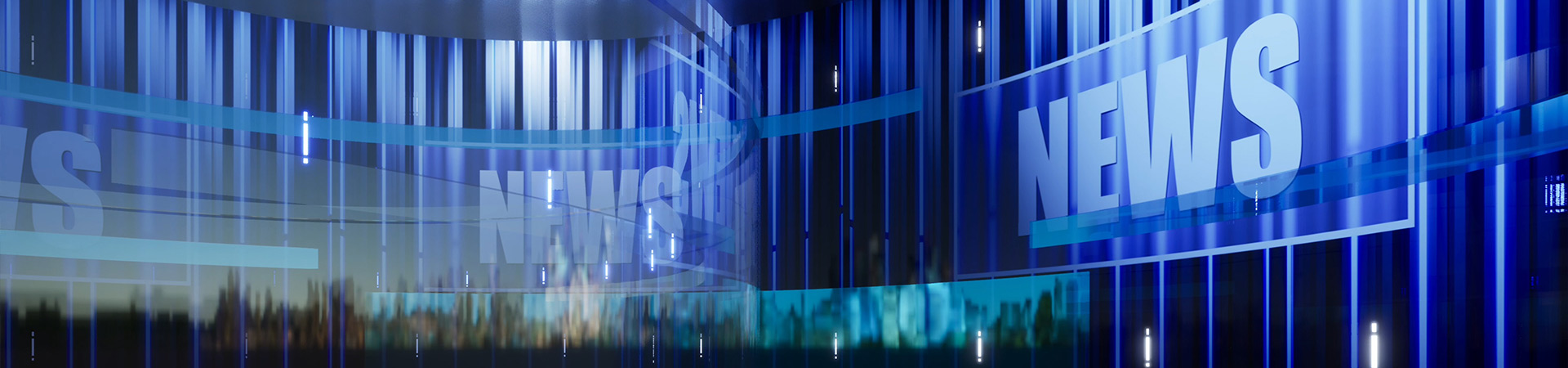
Your Guide to Picking a CNC Oil Mist Collector
CNC oil mist collectors play a pivotal role in achieving this by capturing oil mist, smoke, and fine particulates generated during machining processes.
Table of Contents
Introduction
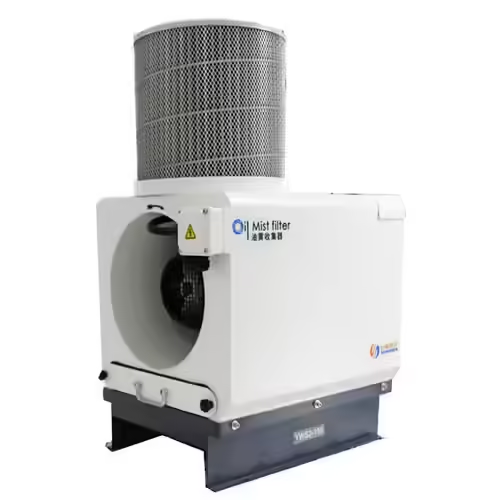
In the fast-paced world of CNC machining, maintaining a clean and safe work environment is critical for both productivity and compliance. CNC oil mist collectors play a pivotal role in achieving this by capturing oil mist, smoke, and fine particulates generated during machining processes. These devices not only improve air quality but also protect equipment, reduce maintenance costs, and ensure worker safety. Shansen, established in 2001 as a leading developer and manufacturer of CNC machine electrical components, recognizes the importance of integrating high-quality CNC oil mist collectors into machining operations. With over two decades of expertise, Shansen is committed to delivering solutions that enhance shop efficiency and safety. This comprehensive guide explores everything you need to know about choosing the right CNC oil mist collector for your operations, from understanding their functionality to evaluating key features for optimal performance.
Why CNC Oil Mist Collectors Are Essential for Your Shop
CNC oil mist collectors are indispensable in modern machine shops due to the health, safety, and operational challenges posed by oil mist. During CNC machining, metalworking fluids interact with high-speed tools, producing oil mist and smoke that can linger in the air. These airborne particles pose respiratory risks to workers, contaminate machinery, and create slippery surfaces, increasing the likelihood of accidents. According to OSHA, exposure to oil mist should not exceed 5 mg/m³ over an 8-hour workday, underscoring the need for effective mist control. By installing a CNC oil mist collector, shops can maintain compliance with regulations, reduce downtime caused by equipment fouling, and create a safer workplace. Shansen’s commitment to innovative CNC solutions aligns with the need for reliable mist collection systems to support long-term operational success.
Health and Safety Benefits of CNC Oil Mist Collectors
The primary benefit of a CNC oil mist collector is its ability to safeguard worker health. Prolonged exposure to oil mist can lead to respiratory issues, skin irritation, and other health problems. A high-quality collector captures these particles at the source, preventing them from dispersing into the shop environment. Additionally, by reducing oil mist buildup on floors and surfaces, these systems minimize slip hazards, enhancing overall shop safety. Shansen’s focus on worker-centric solutions emphasizes the importance of selecting a CNC oil mist collector that prioritizes both air quality and accident prevention.
Equipment Longevity and Maintenance Savings
Oil mist can wreak havoc on CNC machines, clogging filters, damaging circuit boards, and accelerating wear on critical components. A oil mist collector mitigates these issues by removing contaminants before they settle on equipment. This leads to fewer breakdowns, lower maintenance costs, and extended machine lifespans. For shops like those supported by Shansen’s cutting-edge electrical components, integrating a mist collector ensures that machinery operates at peak performance, minimizing costly interruptions.
Types of CNC Oil Mist Collectors
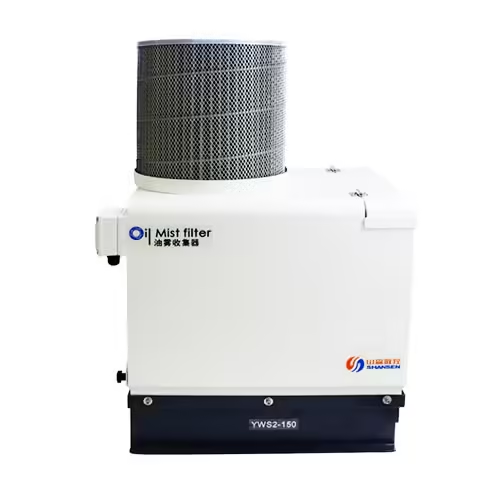
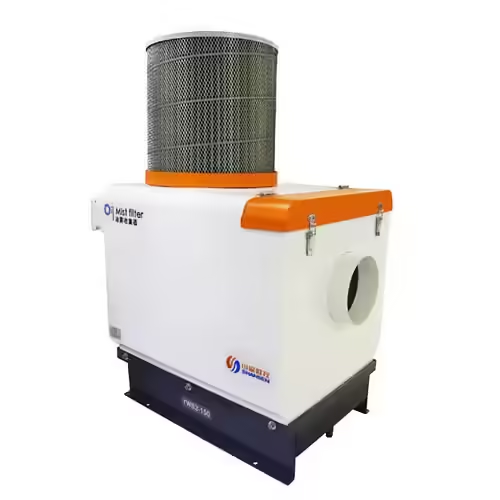
Oil mist collectors come in various designs, each suited to specific machining applications and shop requirements. Understanding the different types is crucial when selecting a system that aligns with your operational needs. Below, we explore the most common technologies used in oil mist collectors.
Centrifugal Oil Mist Collectors
Centrifugal collectors use high-speed rotation to separate oil mist from the air through centrifugal force. These systems are highly effective for a wide range of coolants and mist types, making them versatile for various CNC applications. Their robust design ensures durability, and they typically require minimal maintenance, which is ideal for high-volume shops.
Electrostatic Oil Mist Collectors
Electrostatic precipitators employ electrical charges to capture fine oil mist and smoke particles. These collectors excel at removing submicron particles, making them suitable for high-precision machining processes that generate fine mist. However, they may require more frequent cleaning to maintain efficiency, which is an important consideration for busy shops.
Media-Based Oil Mist Collectors
Media-based collectors rely on filters, such as fiberglass or synthetic media, to trap oil mist particles. These systems are versatile and can handle diverse machining operations, but filter replacement costs and frequency should be factored into the decision-making process. They are often used in shops with moderate mist production.
HEPA-Enhanced Oil Mist Collectors
HEPA filtration systems are designed for environments requiring the highest air quality standards. Often used as a secondary stage in combination with other technologies, HEPA-enhanced oil mist collectors capture ultrafine particles, ensuring compliance with stringent regulations. These are ideal for shops prioritizing worker health and regulatory adherence.
Key Factors to Consider When Choosing a CNC Oil Mist Collector
Selecting the right oil mist collector requires careful evaluation of several factors to ensure it meets your shop’s unique needs. Below is a detailed breakdown of the critical considerations.
Mist Volume and Coolant Type
The volume and type of oil mist generated in your shop significantly influence the choice of collector. High-speed machining with oil-based coolants produces more mist than water-based coolants. Assess your CNC machines’ mist output to determine the collector’s required capacity. For instance, large machining centers may need collectors with higher airflow rates, while smaller lathes may suffice with compact units.
Machine Compatibility
Not all CNC oil mist collectors are compatible with every machine type. Consider the size, speed, and mist production of your CNC equipment. Shansen’s expertise in CNC electrical components highlights the importance of matching the collector to the machine’s specifications to ensure seamless integration and optimal performance.
Airflow and Filtration Efficiency
Airflow capacity, measured in cubic meters per hour (m³/hr), determines how effectively a CNC oil mist collector can process contaminated air. Filtration efficiency, often expressed as a percentage of particles captured, is equally important. Look for collectors with high efficiency for particles as small as 0.3 microns, especially for fine mist and smoke.
Maintenance and Operating Costs
Ease of maintenance is a critical factor, as complex systems can lead to downtime and higher costs. Choose a CNC oil mist collector with accessible filters and long-life components. Additionally, evaluate energy consumption and filter replacement costs to ensure the system is cost-effective over time.
CNC Oil Mist Collector Specifications Comparison Table
To aid in your decision-making process, the following table outlines key specifications to consider when evaluating oil mist collectors. This table focuses on general performance metrics rather than brand-specific comparisons.
Feature | Centrifugal Collectors | Electrostatic Collectors | Media-Based Collectors | HEPA-Enhanced Collectors |
---|---|---|---|---|
Mist Particle Size | 0.5–10 microns | 0.1–5 microns | 0.3–10 microns | 0.01–0.3 microns |
Airflow Range (m³/hr) | 500–3000 | 300–2000 | 400–2500 | 200–1500 |
Maintenance Frequency | Low (every 6–12 months) | Moderate (every 3–6 months) | High (every 1–3 months) | Moderate (every 3–6 months) |
Energy Consumption | Moderate | High | Low | Moderate |
Best For | High-volume shops | Fine mist/smoke | Versatile applications | High air quality standards |
This table provides a snapshot of how different CNC oil mist collectors perform across key metrics, helping you align your choice with your shop’s operational needs.
Installation Tips for CNC Oil Mist Collectors
Proper installation is critical to maximizing the performance of your CNC oil mist collector. Below are actionable tips to ensure a successful setup.
Positioning Your CNC Oil Mist Collector
Mount the collector as close to the mist source as possible, ideally directly on or above the CNC machine. This ensures efficient capture before mist disperses. For larger shops, consider ducting systems to centralize mist collection, but ensure ductwork is properly sealed to prevent leaks.
Ensuring Proper Ventilation
Adequate ventilation is essential to maintain airflow and prevent pressure buildup. Verify that the collector’s exhaust system is compatible with your shop’s ventilation setup. Shansen’s experience in CNC system integration emphasizes the importance of aligning collector installation with existing shop infrastructure.
Regular Maintenance Checks Post-Installation
After installation, establish a maintenance schedule to monitor filter condition, airflow, and system performance. Regular checks prevent clogs and ensure the CNC oil mist collector operates at peak efficiency. Document maintenance activities to track system longevity and identify potential issues early.
How CNC Oil Mist Collectors Enhance Shop Efficiency
Beyond health and safety, CNC oil mist collectors contribute to operational efficiency in several ways. By reducing airborne contaminants, they minimize machine downtime caused by oil buildup, allowing for consistent production schedules. Cleaner air also improves worker morale and productivity, as employees can focus without the distraction of poor air quality. Shansen’s dedication to advancing CNC technology underscores the role of mist collectors in creating streamlined, efficient machining environments.
Reducing Downtime with CNC Oil Mist Collectors
Oil mist buildup can lead to frequent machine cleaning and repairs, disrupting production. A CNC oil mist collector prevents these issues by capturing contaminants at the source, reducing the need for unscheduled maintenance. This is particularly valuable for high-output shops aiming to maximize uptime.
Boosting Worker Productivity
A clean and safe work environment fosters better focus and efficiency among workers. By eliminating the health risks and discomfort associated with oil mist, CNC oil mist collectors create a more productive atmosphere. Shansen’s worker-centric approach aligns with this benefit, emphasizing solutions that enhance both equipment and human performance.
Regulatory Compliance and CNC Oil Mist Collectors
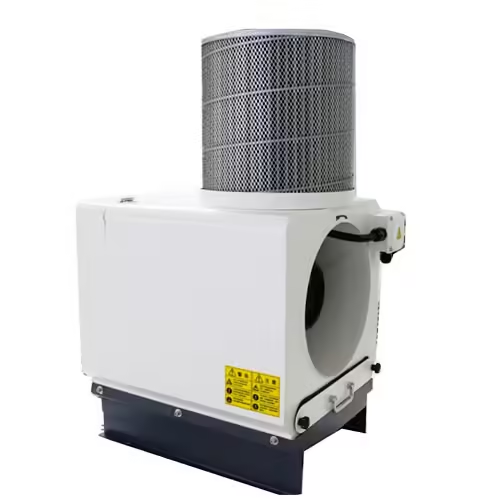
Compliance with workplace safety regulations is non-negotiable in CNC machining. Agencies like OSHA and NIOSH set strict limits on oil mist exposure, and non-compliance can result in fines or legal action. A CNC oil mist collector ensures your shop meets these standards by maintaining air quality within permissible limits. Additionally, some collectors offer monitoring features to track air quality, providing documentation for regulatory audits.
Meeting OSHA and NIOSH Standards
OSHA’s 5 mg/m³ limit for oil mist exposure is a benchmark for shop safety. A high-efficiency CNC oil mist collector ensures compliance by capturing mist and smoke before they reach hazardous levels. Regular maintenance and filter replacements are essential to sustain this performance.
Documentation for Regulatory Audits
Many CNC oil mist collectors come equipped with sensors to monitor filtration efficiency and air quality. These features generate data that can be used to demonstrate compliance during audits, reducing the risk of penalties. Shansen’s expertise in CNC systems highlights the value of integrating such technologies for regulatory adherence.
Conclusion
Selecting the right CNC oil mist collector is a strategic decision that impacts your shop’s safety, efficiency, and compliance. By understanding the types of collectors, evaluating key factors like mist volume and airflow, and prioritizing proper installation and maintenance, you can ensure a cleaner, more productive machining environment. Shansen, with its 24 years of expertise in CNC electrical components, encourages shops to invest in high-quality CNC oil mist collectors to elevate their operations. Ready to enhance your shop’s performance? Contact us today to explore the best CNC oil mist collector solutions for your needs.
FAQ
What is a CNC oil mist collector?
A CNC oil mist collector is a filtration device that captures oil mist, smoke, and particulates generated during CNC machining, improving air quality and protecting equipment.
How often should I maintain my CNC oil mist collector?
Maintenance frequency depends on the collector type and shop usage. Centrifugal collectors may need servicing every 6–12 months, while media-based systems may require filter changes every 1–3 months.
Can a CNC oil mist collector handle all types of coolants?
Most collectors are designed to handle both oil-based and water-based coolants, but compatibility varies. Check the manufacturer’s specifications to ensure the collector suits your coolant type.